StockSteel
Fire-Rated galvanized pipe fittings | UL-Listed Safety Standards
Fire-Rated galvanized pipe fittings | UL-Listed Safety Standards
Couldn't load pickup availability
Fire-Rated Galvanized Pipe Fittings | UL-Listed Safety Standards
Product Specifications (ASTM A795/A795M-21 & UL 1821CRD-2018 Compliance)
Attribute | Details |
---|---|
Material | Malleable Iron (EN-GJMB-350-10/KTH350-10) |
Size Range | 1/4" to 6" (DN 15 to DN 250) |
Pressure Rating | PN16/PN25 (363 PSI/2.5 MPa) |
Temperature Range | -20°C to 200°C (-4°F to 392°F) |
Thread Standard | ISO 7-1, BSPT, NPT |
Surface Treatment | Hot-Dip Galvanized (70+ μm), Electro Galvanized (25+ μm), or Black Finish |
Certifications | UL Listed, FM Approved, ISO 9001, CE, RoHS, CCC |
Tensile Strength | ≥350 MPa |
Elongation | ≥10% |
Hardness | ≤150 HB |
Fire Resistance | 180+ minutes (per UL 1424 & R 53315-2009) |
Packaging | Pallet/Carton (48 cartons per pallet; 20 pallets per 20' container) |
Key Performance Characteristics
-
Tensile Strength & Bend Resistance
Our fittings achieve a minimum tensile strength of 350 MPa, ensuring structural integrity under high-pressure fire suppression systems. This is critical for applications like fire hydrant networks and sprinkler systems, where sudden pressure surges are common. The elongation rate of ≥10% allows the material to absorb mechanical stresses without fracturing. -
Corrosion Protection
Hot-dip galvanizing creates a zinc-iron alloy layer (70+ μm) that resists rust and chemical degradation, even in humid or saline environments. Electro-galvanized options provide a uniform 25+ μm coating for indoor applications. -
Fire Safety Compliance
Tested to UL 1424 and Russian standard R 53315-2009, these fittings maintain functionality for 180+ minutes in fire conditions. The zinc coating acts as a thermal barrier, while the malleable iron core prevents warping. -
Weight Calculation
Use the formula:Example: A 2" (OD 60.3 mm) fitting with 3.9 mm wall thickness weighs approximately 3.2 kg/m.
Why Stainless Steel Resists Rust (and When It Fails)
Stainless steel relies on a chromium oxide layer (passive film) for corrosion resistance. However, rust can occur due to:
- Mechanical Damage: Scratches or abrasions expose the iron substrate to oxygen.
- Chemical Exposure: Chlorides (e.g., seawater) or acids degrade the passive layer.
- Galvanic Corrosion: Contact with dissimilar metals (e.g., carbon steel) accelerates oxidation.
- High Temperatures: Prolonged exposure above 500°C oxidizes chromium, reducing protection.
Our fittings mitigate these risks through:
- Chromium Enrichment (16–20% Cr) for faster oxide layer regeneration.
- Molybdenum Additives to resist pitting in chloride-rich environments.
Applications & Compatibility
- Fire Protection Systems: Compatible with UL-listed sprinklers, FM-approved hydrants, and CPVC pipes.
- Plumbing/Gas Networks: Use pvc to galvanized pipe adapters with dielectric unions to prevent galvanic corrosion.
- Retrofitting: Replacing galvanized pipes? Our fittings reduce labor costs with roll-groove or threaded connections.
Cost Considerations: How Much to Replace Galvanized Pipes?
- Material Costs: 5 per fitting (varies by size and coating).
- Labor Savings: 30–50% faster installation vs. welded carbon steel.
- Lifespan: 50+ years with minimal maintenance, versus 20–30 years for non-galvanized pipes.
Why Choose Our Stainless Steel Solutions?
- Superior Corrosion Resistance: 316L-grade stainless options available for extreme environments (e.g., coastal areas).
- Eco-Friendly: 100% recyclable with ISO 14001-certified production.
- Custom Fabrication: Laser-cut threads and CNC-machined joints ensure leak-proof seals.
- Global Compliance: Meets ASME B16.3, EN 10242, and NFPA standards for cross-border projects.
- Lifetime Warranty: Backed by third-party quality audits and traceable material certifications.
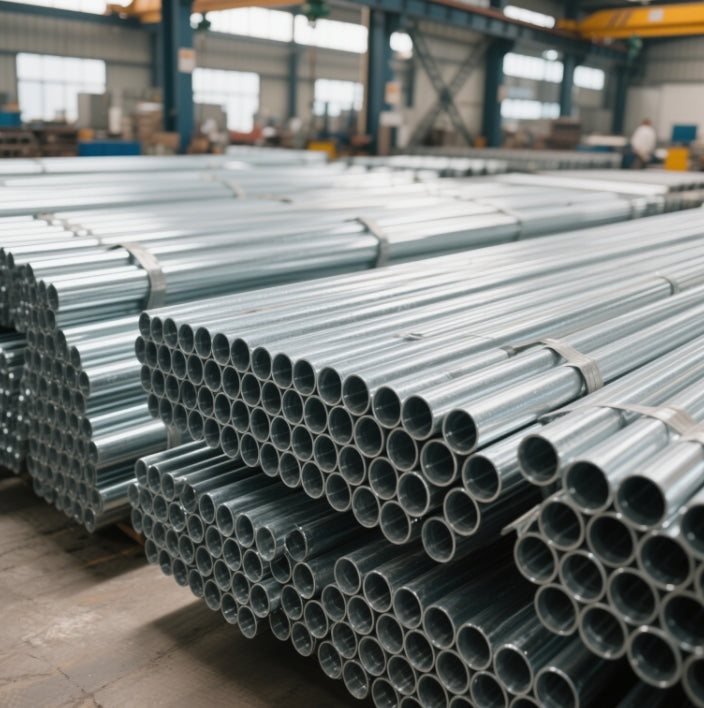