StockSteel
Heavy-Duty galvanized pipe fittings | ASTM-Certified Plumbing Solutions
Heavy-Duty galvanized pipe fittings | ASTM-Certified Plumbing Solutions
Couldn't load pickup availability
Heavy-Duty Galvanized Pipe Fittings | ASTM-Certified Plumbing Solutions
Product Specifications
Industrial-grade galvanized fittings designed for high-pressure and corrosive environments
Parameter | Details |
---|---|
Size Range | 1.5 galvanized pipe (1/2"–6"), 2"–12" (Customizable) |
Material Grade | ASTM A53 Gr.B, BS EN 1562 (EN-GJMB-350-10), KTH350-10 |
Pressure Rating | PN16 (232 PSI) – PN25 (363 PSI) |
Thread Standards | Threaded galvanized pipe: ISO 7-1 (BSPT), BS 21, NPT |
Surface Treatment | Hot-dip galvanized (Zinc coating: 70–120μm), Electro-galvanized (25–50μm) |
Hardness | ≤150 HB (Malleable iron), Tensile Strength: ≥350 MPa |
Certifications | UL Listed, FM Approved, NSF 61, ISO 9001, CE |
Mechanical Properties
Tensile Strength
Heavy-duty threaded galvanized pipe fittings achieve tensile strengths of ≥350 MPa, complying with ASTM A53 and EN 10242 standards. This ensures reliability in high-stress applications like fire sprinkler systems and gas pipelines. For example, EN-GJMB-350-10 malleable iron fittings maintain structural integrity even under cyclic loading.
Bending Strength
Bending strength is 60–70% of tensile strength, allowing fittings to withstand angular stress in HVAC ducts, plumbing networks, and agricultural irrigation systems. Hot-dip galvanized coatings prevent crack propagation under bending loads.
Identification & Standards
Marking Methods
- ASTM A53: Seamless/welded galvanized pipes for general service.
- BS EN 10242: Threaded ends and dimensional tolerances for EU markets.
- ISO 1461: Zinc coating thickness (40–600g/m²) for corrosion resistance.
- UL 6: Compliance for electrical conduit applications.
Weight Calculation
Formula
Weight per meter (kg/m) = (Outer Diameter – Wall Thickness) × Wall Thickness × 0.02466
Example: For a 1.5 galvanized pipe (48.3mm OD, 3mm thickness):
(48.3 – 3) × 3 × 0.02466 = 3.35 kg/m.
Threaded Fittings
- 90° Elbows: Weight = 1.5× standard pipe weight (due to added material at bends).
- Tees: Weight increases by 20–30% compared to straight pipes.
Stainless Steel Corrosion: Causes & Prevention
Why Does Stainless Steel Rust?
- Chloride Exposure: Coastal or industrial environments cause pitting in grades like 304/316L.
- Mechanical Damage: Scratches from tools expose the base metal to oxidation.
- Improper Welding: Inadequate argon shielding during welding creates chromium-depleted zones.
- Low-Quality Alloys: Substandard 430 stainless steel lacks sufficient nickel for corrosion resistance.
Key Comparisons & Risks
threaded galvanized pipe
- Applications: Ideal for gas lines, fire sprinklers, and water supply due to leak-proof BSPT/NPT threads.
- Installation: No welding required—sealants like PTFE tape ensure pressure integrity.
will galvanized pipe rust
While hot-dip galvanized coatings (70–120μm) resist corrosion for 40–70 years, acidic soils or saltwater accelerate zinc depletion. Rust spots may form if the coating is scratched or exposed to pH <6.
1.5 galvanized pipe
- Dimensions: 48.3mm OD, wall thickness 1.8–4.5mm.
- Use Cases: Residential plumbing, compressed air systems, and greenhouse frameworks.
Why Choose Our Stainless Steel Products?
- Zero Rust Guarantee: Our 304/316L stainless steel outperforms galvanized pipes in chloride-rich or acidic environments, with a 50+ year lifespan.
- Hygienic Design: Non-porous surfaces prevent bacterial growth, compliant with NSF 61 for potable water.
- Eco-Friendly: 100% recyclable with no toxic lead residues—unlike older galvanized pipes.
- Certified Durability: ISO 9001, CE, and UL certifications ensure compliance with global safety standards.
- Custom Solutions: Tailored threading (BSPT/NPT), lengths (5.8m–18m), and alloy blends (duplex, superaustenitic).
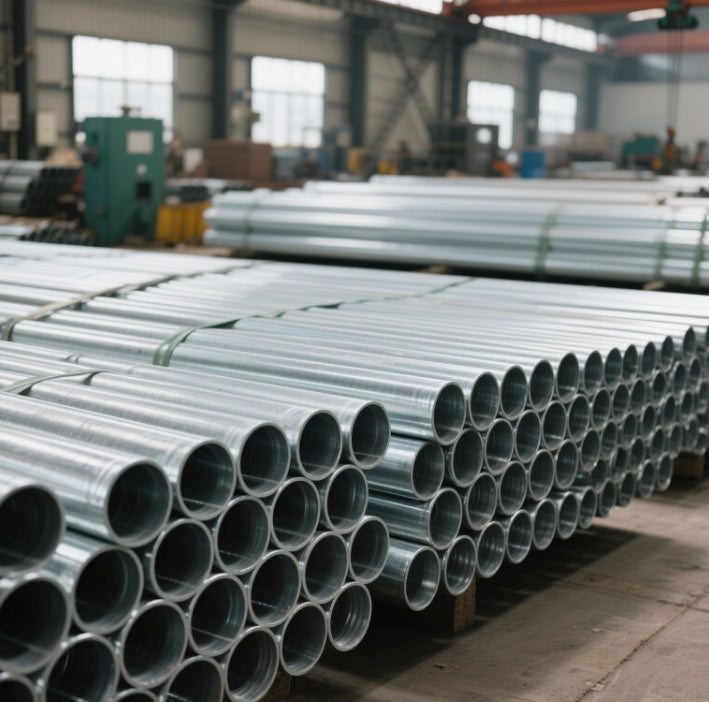