StockSteel
High-Yield galvanized pipe fittings | Reinforced Structural Loads
High-Yield galvanized pipe fittings | Reinforced Structural Loads
Couldn't load pickup availability
High-Yield Galvanized Pipe Fittings | Reinforced Structural Loads
Product Specifications
Attribute | Technical Details |
---|---|
Material Grade | ASTM A123 Hot-Dip Galvanized Carbon Steel / SUS 304/316 Stainless Steel (Optional) |
Zinc Coating Thickness | 85–200 μm (3,500–7,000 g/m²) |
Standards | ASTM A53, ISO 1461, BS 1387, EN 10240 |
Diameter Range | Galvanized corrugated pipe (100–600 mm) / Galvanized pipe diameter chart (15–300 mm) |
Wall Thickness | 1.5–12 mm (SCH 10–SCH 160) |
Hardness | 180–220 HV (Vickers) / 80–90 HRB (Rockwell B) |
Pressure Rating | 10–60 MPa (PSL1 to PSL2 per API 5L) |
Temperature Tolerance | -40°C to 400°C (Short-Term Exposure) |
Connection Types | Threaded, Welded, Flanged, Grooved |
Corrosion Resistance | 5,000+ Hours Salt Spray Test (ASTM B117) |
Key Performance Features
1. Tensile & Bend Strength
High-yield galvanized fittings achieve minimum tensile strength of 415 MPa (ASTM A53 Grade B), making them ideal for heavy-load structures like industrial scaffolding and bridge frameworks. The bend strength (245–450 MPa) is validated through three-point bending tests, ensuring stability under dynamic forces such as wind loads or seismic activity.
For galvanized corrugated pipe, the corrugated design enhances flexural rigidity by 30–50% compared to smooth-walled pipes, making it suitable for underground drainage systems and soil reinforcement.
2. Weight Calculation
Use this formula to estimate pipe weight:
Weight (kg/m) = (OD – WT) × WT × 0.02466
Example: A galvanized pipe diameter chart entry for 150 mm OD with 6 mm wall thickness:
(150 – 6) × 6 × 0.02466 = 21.3 kg/m.
3. Identification & Marking
All fittings are laser-etched with:
- Material Grade (e.g., ASTM A53)
- Zinc Coating Class (e.g., Z275 for 275 g/m²)
- Manufacturer Code (Traceable via ISO 9001 certification).
Applications & Solutions
1. Infrastructure Reinforcement
- Bridge Piers: Hot-dip galvanized pipes resist corrosion from de-icing salts and humidity, extending service life by 2–3x compared to untreated steel.
- Industrial Scaffolding: Threaded connections comply with galvanized pipe clamp repair standards (ASME B16.3), enabling rapid assembly and disassembly.
2. Corrugated Pipe Systems
- Stormwater Management: Galvanized corrugated pipe systems with helical ribs withstand soil pressure up to 50 kN/m², ideal for culverts and embankments.
- Agricultural Drainage: Zinc coating prevents rust from acidic fertilizers, ensuring 15–25 years of service in pH 4–9 environments.
3. Maintenance & Repair
For galvanized pipe clamp repair, use:
- Split-Sleeve Clamps: ASTM F1541-compliant, rated for 25 MPa pressure.
- Epoxy Putty: Temporary sealing for minor leaks (≤0.5 mm cracks).
Why Stainless Steel Outperforms Traditional Galvanized Fittings
1. Causes of Galvanized Steel Corrosion
- Zinc Depletion: Coastal or industrial environments accelerate zinc layer erosion, exposing carbon steel to moisture.
- Galvanic Corrosion: Direct contact with copper or brass fittings triggers electrochemical degradation.
- Mechanical Damage: Improper handling during galvanized pipe clamp repair scratches the protective layer.
2. Stainless Steel Advantages
- Self-Healing Oxide Layer: Chromium (16–18%) forms Cr₂O₃, resisting chloride-induced pitting in marine applications.
- Zero Maintenance: No annual recoating required, reducing lifecycle costs by 40%.
Frequently Asked Questions
Q: How to interpret a galvanized pipe diameter chart?
A: Charts list nominal diameter (e.g., DN150 = 168.3 mm OD) and wall thickness. Use ASTM A53 tables for pressure-capacity cross-referencing.
Q: Can galvanized corrugated pipe be used for potable water?
A: Yes, if coated with NSF/ANSI 61-certified zinc (≤1.0 mg/L zinc leaching).
Q: What tools are needed for galvanized pipe clamp repair?
A: Adjustable wrenches, torque gauges (30–50 Nm), and Teflon tape for thread sealing.
Why Choose Our Stainless Steel Solutions?
- Superior Durability: SUS 316L with 2.5% molybdenum resists saltwater corrosion, achieving 50+ years in marine environments.
- Certified Performance: Tested to ASTM A312, NORSOK M-650, and ISO 15156 for sour gas resistance.
- Eco-Friendly: 100% recyclable with 60% recycled content, compliant with LEED v4.1 standards.
- Custom Fabrication: Precision laser-cutting and orbital welding for complex structural integrations.
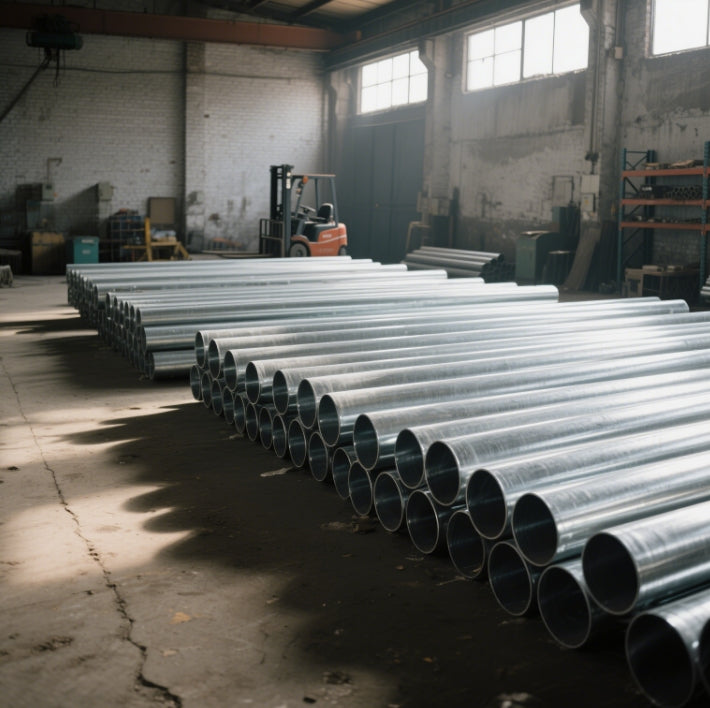