StockSteel
Impact-Resistant galvanized pipe | Reinforced Steel for Heavy Loads
Impact-Resistant galvanized pipe | Reinforced Steel for Heavy Loads
Regular price
$590.00 SGD
Regular price
Sale price
$590.00 SGD
Unit price
per
Taxes included.
Shipping calculated at checkout.
Couldn't load pickup availability
Impact-Resistant Galvanized Pipe | Reinforced Steel for Heavy Loads
Product Specifications
Parameter | Details |
---|---|
Material | Low-carbon steel (Q235, Q345) with hot-dip galvanized coating (70–300 g/m² zinc) |
Standards | ASTM A53, EN10219, ISO 9001, BS1387 |
Diameter Range | 1/2" (21.3 mm) to 12" (323.9 mm) for galvanized steel pipe water systems |
Wall Thickness | 1.0–6.0 mm (customizable for high-pressure applications) |
Length | Standard: 6 m, 12 m; Custom: 1–12 m (compatible with sharkbite for galvanized pipe fittings) |
Surface Finish | Smooth spangled finish (hot-dip galvanized) or matte for industrial use |
Hardness | Rockwell B scale: G350–G550 (suitable for structural and heavy-load uses) |
Max. Working Pressure | 450 psi (3.1 MPa) |
Key Attributes
-
Superior Corrosion Resistance:
- The hot-dip galvanizing process forms a zinc-iron alloy layer, offering 4–6× longer lifespan than galvanized vs black pipe alternatives. Ideal for coastal, chemical, and high-humidity environments.
- Zinc coating acts as a "sacrificial layer," protecting the base steel even if scratched.
-
Impact Resistance:
- Tensile Strength: 330–550 MPa (Grade Q345 recommended for heavy-duty frameworks).
- Bend Strength: Withstands 180° bending without cracking (tested per ASTM A370).
-
Versatility:
- Compatible with sharkbite for galvanized pipe fittings for leak-proof connections in plumbing, HVAC, and gas systems.
- Suitable for structural columns, water pipelines, and industrial machinery.
Manufacturing Process
Stage | Description |
---|---|
Material Prep | Steel coils pickled to remove oxides and fluxed for optimal zinc adhesion. |
Pipe Formation | High-frequency induction welding (HFIW) ensures seamless joints for high-pressure use. |
Galvanizing | Immersion in molten zinc (450–465°C) to create a uniform, corrosion-resistant layer. |
Quality Control | Hydrostatic testing (1.5× working pressure) and salt spray compliance (5,000+ hours). |
Technical Specifications
1. Tensile & Bend Strength
- Tensile Strength: Ranges from 330 MPa (Grade Q195) to 550 MPa (Grade Q345). Higher grades are ideal for load-bearing structures like bridges and industrial frameworks.
- Bend Strength: Achieves a minimum bend radius of 2.5× pipe diameter without fracture (ISO 8491 compliance).
2. Weight Calculation
Formula for galvanized pipe weight:
- Example: A galvanized steel pipe water line with 88.9 mm OD and 4.0 mm WT weighs ~8.3 kg/m.
3. Identification Marking
- Pipes are stamped with:
- Manufacturer’s logo and ASTM standard (e.g., ASTM A53).
- Size (e.g., galvanized vs black pipe compatibility).
- Coating type (HDG for hot-dip) and production batch code.
4. Stainless Steel Rust Causes
While stainless steel resists rust due to a chromium oxide layer, corrosion can occur due to:
- Chloride Exposure: Coastal environments or de-icing salts accelerate pitting (common in vent pipe systems).
- Mechanical Damage: Scratches or welding disrupt the oxide layer, exposing the substrate to oxidation.
- Chemical Contamination: Acids or alkalis (e.g., industrial pollutants) degrade protective layers.
Why Choose Our Galvanized Pipes?
- Bulk Pricing Advantage: Competitive rates for structural and water pipeline projects (FOB: $700–900/ton).
- Custom Solutions: Precision threading for sharkbite for galvanized pipe fittings and pre-cut lengths.
- Certified Quality: ISO 9001, RoHS, and ASTM compliance with 5,000+ hours of salt spray testing.
- Global Logistics: Sea-worthy packaging and 15–30 day delivery worldwide.
Why Stainless Steel Stands Out
While galvanized pipes excel in cost-effectiveness, our stainless steel products offer unmatched longevity for specialized applications:
- Superior Corrosion Resistance: Chromium-nickel alloys (e.g., SUS 304/316) resist rust even in acidic or marine environments.
- Hygienic & Aesthetic: Non-porous surface prevents bacterial growth, ideal for food processing and architecture.
- Low Maintenance: No recoating required, reducing lifecycle costs by 30% compared to galvanized options.
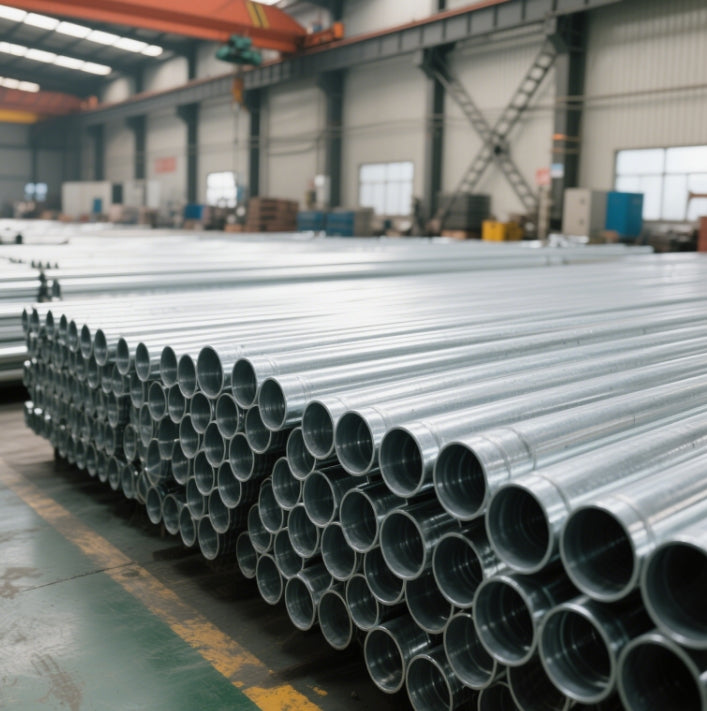