StockSteel
Marine-Grade galvanized pipe fittings | Saltwater Corrosion Resistance
Marine-Grade galvanized pipe fittings | Saltwater Corrosion Resistance
Couldn't load pickup availability
Marine-Grade Galvanized Pipe Fittings | Saltwater Corrosion Resistance
Product Specifications
Attribute | Technical Details |
---|---|
Material Grade | ASTM A123 Hot-Dip Galvanized Carbon Steel / SUS 316 Stainless Steel (Marine Grade) |
Zinc Coating Thickness | 85–120 μm (3,500–4,200 g/m²) |
Standards | ISO 1461, ASTM A153, EN 10240, NORSOK M-650 |
Diameter Range |
1 inch galvanized pipe 20 ft to 8 galvanized pipe (Custom lengths up to 12m) |
Wall Thickness | SCH 10–SCH 160 (1.2–15 mm) |
Hardness | 180–220 HV (Vickers) |
Pressure Rating | 10–60 MPa (PSL1 to PSL2 per API 5L) |
Temperature Tolerance | -40°C to 400°C (Short-Term Exposure) |
Thread Compatibility | NPT, BSPT, BSPP (Meets ANSI/ASME B1.20.1) |
Saltwater Test Compliance | ASTM B117 (5,000+ Hours Salt Spray Resistance) |
Key Performance Features
1. Tensile & Bend Strength
Marine-grade galvanized fittings achieve minimum tensile strength of 415 MPa (ASTM A53 Grade B), ensuring structural integrity in high-pressure marine environments like offshore platforms and ship hulls. The bend strength (245–450 MPa) is validated through three-point bending tests, making them ideal for dynamic applications such as wave-impact zones and ballast systems.
2. Corrosion Resistance
The hot-dip galvanizing process creates a metallurgical bond between zinc and steel, offering 4x longer lifespan than electroplated alternatives. For extreme salinity, SUS 316 stainless steel variants incorporate 2.5% molybdenum to resist pitting corrosion in chloride-rich seawater.
3. Weight Calculation
Use this formula to estimate pipe weight:
Weight (kg/m) = (OD – WT) × WT × 0.02466
Example: 8 galvanized pipe (219 mm OD, 6 mm WT):
(219 – 6) × 6 × 0.02466 = 31.6 kg/m.
Critical Applications
- Ship Plumbing: Complies with DNV-GL & ABS standards for potable water and fuel lines.
- Coastal Infrastructure: Resists salt spray in piers, docks, and desalination plants.
- Offshore Oil Rigs: Withstands hydrogen sulfide corrosion in subsea pipelines.
Why Stainless Steel Outperforms Traditional Options
1. Galvanized vs. Black Pipe vs. Stainless Steel
Factor | Galvanized | Black Pipe | Stainless Steel |
---|---|---|---|
Corrosion Resistance | Moderate (Zinc layer erosion over time)
6
|
None (Prone to rust) | Exceptional (Passive oxide layer)
19
|
Lifespan | 15–25 years | 5–10 years | 50+ years |
Maintenance | Annual inspections | Frequent replacements | Minimal |
Cost Efficiency | Low upfront cost | Lowest initial cost | Higher initial, lower lifecycle cost |
2. Causes of Stainless Steel Corrosion
While rare, corrosion may occur due to:
- Chloride Stress Corrosion Cracking (CSCC): Aggressive in seawater >60°C.
- Galvanic Coupling: Avoid pairing with black pipe or copper alloys without dielectric insulation.
- Mechanical Damage: Scratches exposing base metal to saltwater.
Frequently Asked Questions
Q: How does galvanized pipe compare to stainless steel in saltwater?
A: Galvanized pipe provides cost-effective protection for moderate salinity (e.g., freshwater mix), while stainless steel is mandatory for pure seawater or chemical exposure.
Q: Can I thread 1 inch galvanized pipe 20 ft onsite?
A: Yes! Use ratchet threaders with cutting oil and follow ASME B1.20.1 specs for NPT threads.
Q: What’s the maximum salinity tolerance?
A: Galvanized fittings withstand up to 35,000 ppm salinity (typical seawater). For hypersaline environments (>50,000 ppm), upgrade to SUS 316L.
Why Choose Our Stainless Steel Solutions?
- Superior Material Science: 16–18% chromium + 10–12% nickel alloy matrix prevents biofilm formation, critical for marine drinking water systems.
- Certified Performance: Validated per NORSOK M-650
and ISO 15156 for sour service environments. - Eco-Conscious: 100% recyclable with 60% recycled content, aligning with LEED v4.1 standards.
- Custom Fabrication: Laser-cut threads and orbital welding for precision-fit installations.
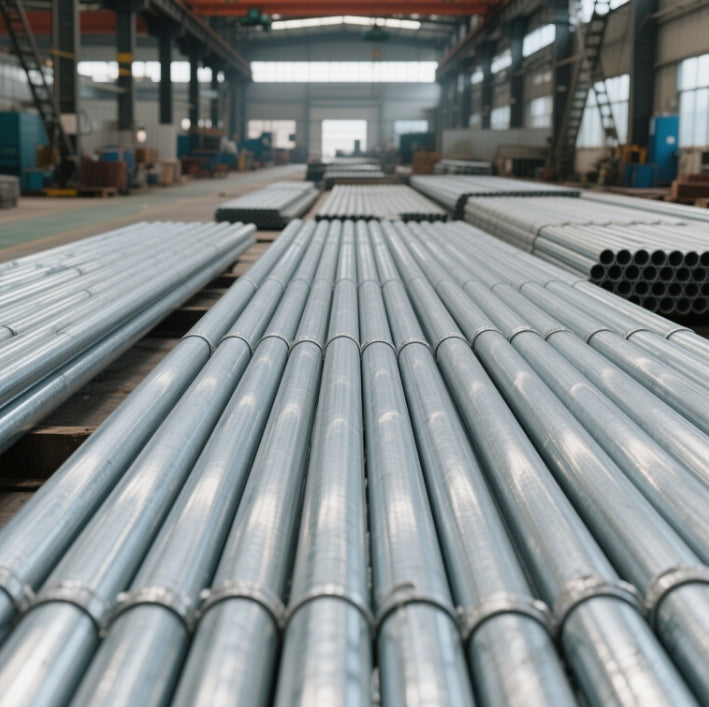