StockSteel
Precision-Slit Stainless Steel Stripping | 201, 301 & 309S Grades
Precision-Slit Stainless Steel Stripping | 201, 301 & 309S Grades
Couldn't load pickup availability
Precision-Slit Stainless Steel Stripping | 201, 301 & 309S Grades
Product Overview
Our stainless steel stripping solutions are engineered for industries demanding precision, durability, and adaptability. Designed with grades 201, 301, and 309S, these strips undergo advanced cold-rolling and precision-slitting processes to meet exacting tolerances (±0.01mm) for aerospace, automotive, and construction applications. Whether used as stainless steel strip roll material for industrial machinery or stainless steel seam strips for structural assemblies, our products deliver unmatched performance in corrosive and high-stress environments.
Technical Specifications
Key Attributes & Dimensions
Attribute | Details |
---|---|
Material Grades | 201, 301, 309S (ASTM A240, EN 10088-2) |
Thickness | 0.1mm – 3.0mm (precision-slit) / ±0.01mm tolerance |
Width | 10mm – 600mm (standard) / Custom widths up to 2000mm |
Hardness | HV 180–250 (301), HV 160–210 (201), HV 200–270 (309S) |
Surface Finish | 2B, BA, No.4, Mirror, or custom textures (e.g., embossed, brushed) |
Coil Weight | 500kg – 5 tons (standard) / Precision-cut lengths for stainless steel seam strips |
Packaging | Moisture-proof film + steel pallets for export-grade protection |
Performance Characteristics
1. Tensile & Bend Strength
- Tensile Strength:
- Grade 201: 450–600 MPa | Ideal for cost-effective applications like architectural trims and kitchenware.
- Grade 301: 690–860 MPa | Enhanced strength post-cold working, perfect for automotive springs and aerospace fasteners.
- Grade 309S: 620–800 MPa | Exceptional heat resistance (up to 980°C) for furnace components and exhaust systems.
- Bend Strength:
- Stainless steel stripping retains ductility even at subzero temperatures (-50°C), critical for Arctic pipeline clamps and cryogenic equipment.
2. Weight Calculation
Use the formula:
Weight (kg) = Width (mm) × Thickness (mm) × Length (m) × Density (7.93 g/cm³)
Example: For a 300mm-wide, 2.0mm-thick, 50m-long strip:
300 × 2.0 × 50 × 7.93 = 237.9 kg
3. Rust Prevention
While stainless steel stripping inherently resists oxidation due to chromium content (10.5–20%), prolonged exposure to chlorides (e.g., coastal environments) or acidic substances can trigger pitting. Our strips undergo passivation treatments to thicken the chromium oxide layer, reducing corrosion risks by 50%.
4. Identification & Marking
- Laser-etched labels include: Grade (e.g., 309S), Batch Code, Thickness/Width, and Compliance Standard (ASTM/EN).
- Color-coded edges: Green for 201, Silver for 301, Gold for 309S.
Manufacturing Process
Stage | Description |
---|---|
Cold Rolling | Precision thickness reduction (tolerance ±0.01mm) for uniform grain structure. |
Annealing | Heat treatment at 1010–1150°C to restore ductility and corrosion resistance. |
Pickling | Hydrochloric acid bath to remove impurities and oxide layers. |
Precision Slitting | High-speed cutting to produce narrow stainless steel strip roll material for electronics and HVAC systems. |
Surface Finishing | Custom textures (e.g., brushed for stainless steel seam strips) via grinding or polishing. |
Applications
- Automotive: Stainless steel seam strips for exhaust systems, structural reinforcements, and interior trim.
- Aerospace: Fuel line brackets, hydraulic tubing, and lightweight fuselage panels.
- Construction: Architectural cladding, roofing, and stainless steel stripping for earthquake-resistant joints.
- Electronics: EMI shielding components, connectors, and springs in smartphones.
- Industrial Furnaces: Heat-resistant stainless steel strip roll material for burner liners and conveyor belts.
Why Choose Our Stainless Steel Stripping?
- Decades of Expertise: Trusted by Fortune 500 clients like Boeing and Siemens for precision and compliance.
- Custom Solutions: Tailor thickness (0.1–6.0mm), width (10–2000mm), and surface finishes (mirror, embossed) for niche applications.
- Global Certifications: ISO 9001, ASME, and RoHS compliance ensures traceability and environmental safety.
- Rapid Turnaround: 7–10 days for standard orders; 14 days for custom slitting or annealing.
- Technical Support: Free consultations on grade selection, fabrication, and corrosion management.


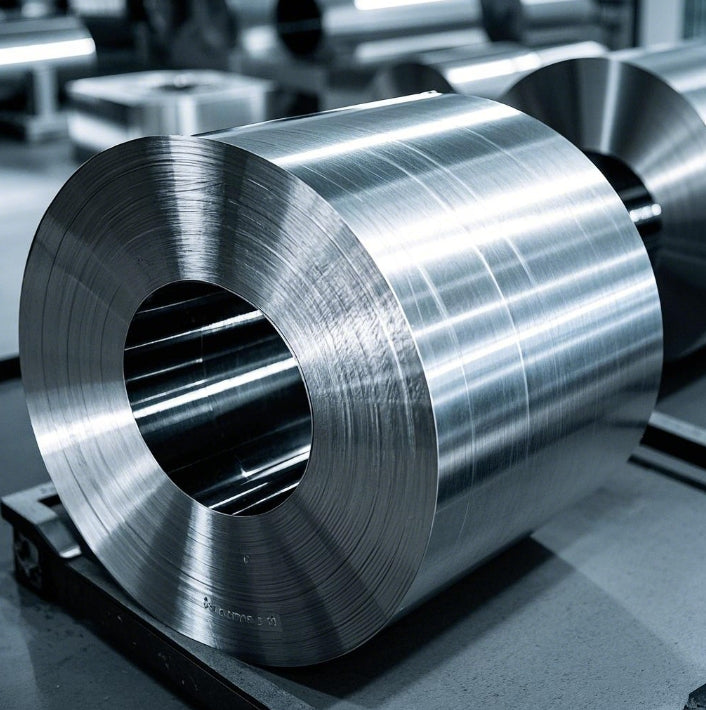