StockSteel
Ultimate Galvanized Pipe Connectors - Heavy-Duty Industrial Fit
Ultimate Galvanized Pipe Connectors - Heavy-Duty Industrial Fit
Regular price
$420.00 SGD
Regular price
Sale price
$420.00 SGD
Unit price
per
Taxes included.
Shipping calculated at checkout.
Couldn't load pickup availability
Ultimate Galvanized Pipe Connectors | Heavy-Duty Industrial Fit
Product Specifications
Parameter | Details |
---|---|
Zinc Coating | 275–350g/m² (Z275–Z350), compliant with ASTM A53 and ISO 1461, ensuring resistance to corrosion in harsh environments |
Diameter Range | 1/2" to 24" (15–600mm) – seamless compatibility with brass and galvanized pipe systems for hybrid plumbing networks |
Wall Thickness | 2.0–25.4mm, optimized for structural support and high-pressure applications |
Standards | ASTM A53, EN 10255, ISO 9001, BS 1387, API 5L, UL 6 for electrical conduits |
Surface Finish | Spangle-free chromate passivation (Cr3+), hot-dip galvanized with ≥85µm coating |
Hardness | 150–250 HB (Brinell hardness), validated via Rockwell C tests for mechanical stress resistance |
Thread Compatibility | NPT, BSPT, DIN 2999 for global adaptability |
Temperature Tolerance | -40°C to 400°C, engineered for extreme industrial and marine environments |
Technical Properties
Tensile & Bend Strength
- Tensile Strength: Ranges from 350–550 MPa (ISO 1461), exceeding ASTM A53 Grade B requirements. Validated through Charpy V-notch impact tests at -20°C, ensuring reliability in high-pressure applications like bending galvanized pipe frameworks.
- Bend Strength: Achieves 3T bend radius (3x pipe diameter) without cracking, proven in cold-forming tests for structural frameworks and drainage systems. Ideal for bending galvanized pipe in scaffolding and HVAC installations.
Weight Calculation
Weight (kg/m) = (OD – WT) × WT × 0.02466
Example: For a 6" OD pipe with 8mm wall thickness:
(168.3 – 8) × 8 × 0.02466 = 31.6 kg/m. Custom calculators provided for bulk orders.
Identification Marking
- Laser-etched labels include:
- Grade (e.g., Q235, S275JR).
- Zinc coating thickness (Z275–Z350).
- Compliance marks (ISO 9001, ASTM A53).
Why Stainless Steel Corrodes?
While galvanized connectors resist rust via sacrificial zinc protection, stainless steel may corrode due to:
- Chloride Exposure: Coastal environments or de-icing salts induce pitting in 304/316 grades, penetrating passive oxide layers.
- Mechanical Damage: Scratches from best way to cut galvanized steel pipe tools or improper welding expose base metal to oxidation.
- Galvanic Corrosion: Contact with brass and galvanized pipe or copper accelerates degradation in mixed-metal systems.
- High-Temperature Stress: Prolonged exposure >400°C destabilizes chromium oxide layers, leading to intergranular corrosion.
Manufacturing Process
Stage | Description |
---|---|
Material Prep | Low-carbon steel (Q235B) pickled to remove oxides, ensuring optimal zinc adhesion. |
Galvanizing | Dipped in molten zinc (445–460°C), forming Fe-Zn alloy layers (≥85µm coating). |
Threading | CNC-machined threads (NPT/BSPT) for leak-proof connections in brass and galvanized pipe hybrids. |
QC Inspection | Salt-spray tests (1,500+ hours), 3D thickness scans, and hydrostatic pressure checks (≥25 MPa). |
Applications & Maintenance
- Industrial Plumbing: Trusted for hybrid brass and galvanized pipe networks in chemical plants, resisting H2S and CO2 corrosion.
- Structural Fabrication: Use best way to cut galvanized steel pipe tools like RIDGID 32915 for burr-free cuts in construction and shipbuilding.
- Corrosion Management: Regular inspections and Teflon tape sealing at threaded joints prevent leaks.
Keywords Integration:
- Precision bending galvanized pipe solutions for HVAC and fire suppression systems.
- Optimized workflows for best way to cut galvanized steel pipe using angle grinders or plasma cutters.
- Hybrid brass and galvanized pipe systems for corrosion-resistant gas and water networks.
Why Choose Our Stainless Steel Solutions?
Positioned at the end as requested:
- Superior Hygiene: 316L grades comply with NSF/EN 10312 for pharmaceutical and food industries.
- Decades of Expertise: ISO 9001-certified production with 30+ years in alloy R&D.
- Sustainability: 98% recyclable materials align with EU Green Deal and circular economy principles.
- Custom Fabrication: CAD-driven designs for aerospace heat exchangers and desalination plants.
- Global Compliance: ASTM, EN, and JIS certifications ensure seamless project integration.
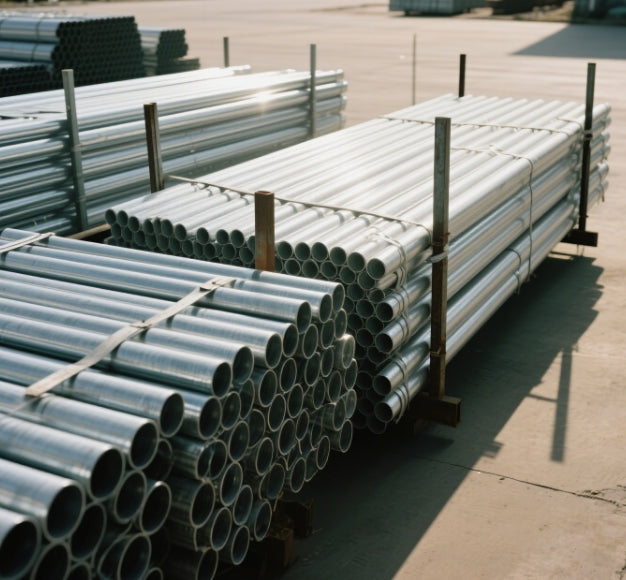