StockSteel
Ultimate Galvanized Steel Pipe | Hot-Dip Coated Water & Gas Solutions
Ultimate Galvanized Steel Pipe | Hot-Dip Coated Water & Gas Solutions
Couldn't load pickup availability
Ultimate Galvanized Steel Pipe | Hot-Dip Coated Water & Gas Solutions
Product Overview
Our galvanized steel pipe series combines advanced hot-dip galvanizing technology with precision engineering, offering unparalleled corrosion resistance and durability for water, gas, and industrial applications. Certified to API, CE, BSI, TISI, JIS, and ISO9001 standards, these pipes ensure compliance with global quality benchmarks.
Technical Specifications
Parameter | Details |
---|---|
DN (Diameter Nominal) | 6, 8, 10, 15, 20, 25, 32, 40, 50, 65, 80, 100, 125, 150 |
Outer Diameter (mm) | 10.2–165 (±0.5mm to ±1% tolerance) |
Thickness Range (mm) | 1.24–59.24 (Standard: 2.0–5.5; Thickened: 2.5–5.5) |
Zinc Coating | 40–275 g/m² (Z40–Z275), ensuring uniform adhesion and long-term protection. |
Hardness (Rockwell) | 60–70 HRB (Cold-rolled base steel) |
Surface Treatment | Chromed (Cr³⁺/Cr⁶⁺), oiled/dry, skin-passed for enhanced smoothness. |
Mechanical Properties
-
Tensile Strength:
- Minimum 520 MPa, achieved through hot-dip galvanizing and alloy optimization. The zinc-iron alloy layer enhances structural integrity, making the galvanized steel pipe ideal for high-pressure systems.
-
Bending Strength:
- Withstands **≥205 MPa yield strength**, ensuring flexibility without deformation. Suitable for curved installations in gas pipelines or architectural frameworks.
Identification & Standards
- Marking Method: Pipes are laser-etched with codes indicating grade (e.g., SGCC, DX51D), thickness, coating weight (e.g., Z180), and certification (CE, JIS).
- Compliance: Meets ASTM A653 (spangle types: regular/minimized/zero), EN10142, and G3302 for international compatibility.
Weight Calculation Formula
Weight per meter (kg/m) = , where:
- = Outer diameter (mm)
-
= Wall thickness (mm)
Example: A galvanized water pipe with OD=60mm and WT=4.5mm weighs .
Why Does Stainless Steel Rust?
While stainless steel inherently resists corrosion due to its chromium-rich oxide layer (12–18% Cr), certain conditions can cause rusting:
- Chloride Exposure: Saltwater or de-icing agents degrade the passive layer, leading to pitting corrosion.
- Mechanical Damage: Scratches or welding can expose untreated steel to moisture.
- Low-Quality Alloys: Substandard grades (e.g., <8% Ni in 304 steel) reduce oxidation resistance.
Manufacturing Process
Step | Description |
---|---|
Pickling | Acid wash removes mill scale and impurities for optimal zinc adhesion. |
Fluxing | Immersion in ammonium/zinc chloride solution to prevent re-oxidation. |
Hot-Dip Galvanizing | Submersion in molten zinc (680°F) forms a metallurgical bond with the steel substrate. |
Cooling & Finishing | Quenched in water, followed by chromate passivation or oiling for added protection. |
Applications
- Galvanized water pipe: Ideal for municipal water supply, HVAC systems, and fire sprinklers.
- Galvanized pipe fittings: Corrosion-resistant elbows, tees, and couplings for industrial plumbing.
- Structural frameworks, agricultural equipment, and solar panel supports.
Why Choose Our Stainless Steel Solutions?
While our galvanized steel pipes excel in corrosion resistance, our stainless steel products offer additional advantages for extreme environments:
- Food-Grade Safety: 304 stainless steel (18% Cr, 8% Ni) is non-toxic and NSF-certified for kitchenware and medical devices.
- Aesthetic Versatility: Mirror polish, brushed finishes, or colored coatings enhance architectural designs.
- Lifespan Guarantee: 30+ years of service with minimal maintenance, even in coastal or chemical zones.
- Eco-Friendly: 100% recyclable and free from VOC emissions, aligning with green building standards.
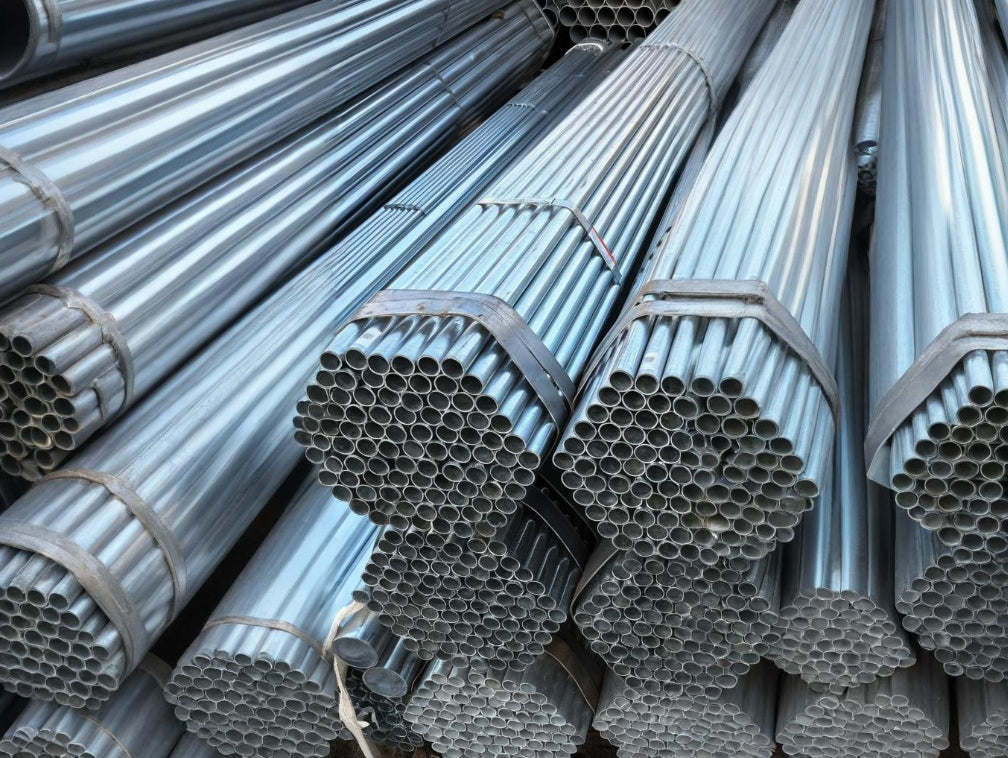
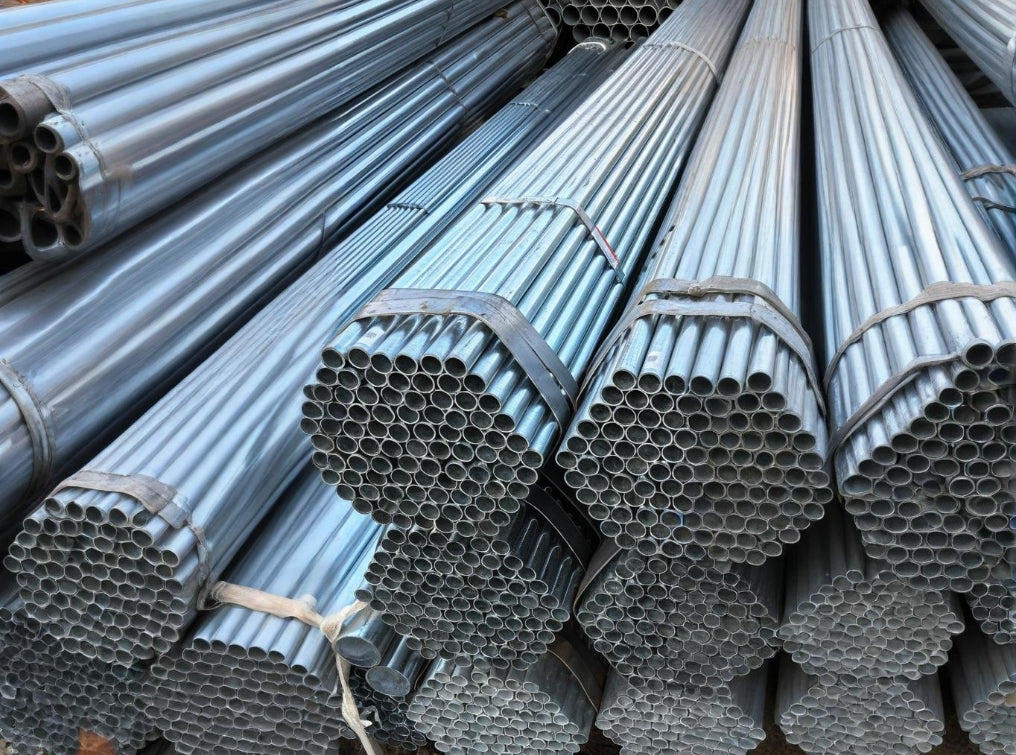